NSK reduces machine tool quadrant glitches
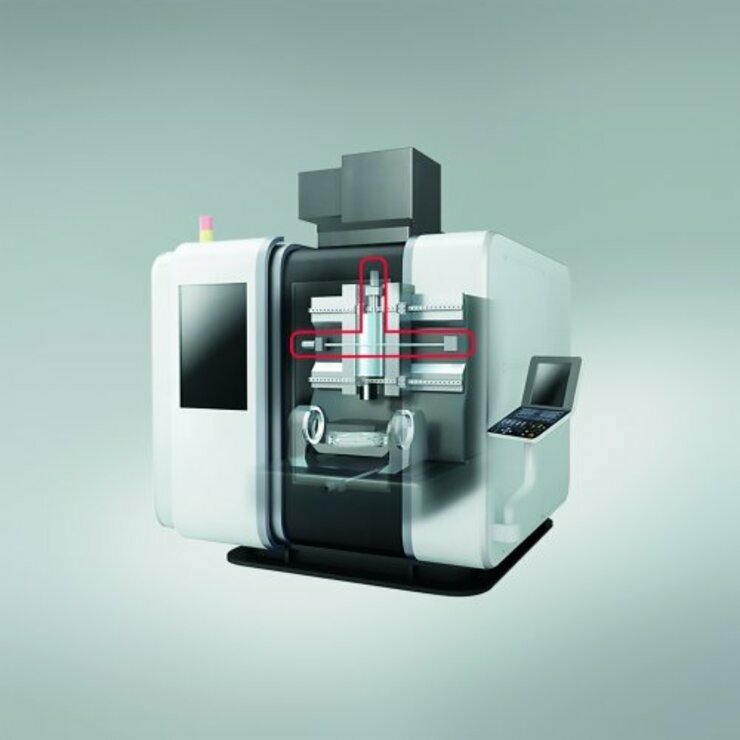
The occurrence of machine tool quadrant glitches during circular interpolation
routines are an established issue. Thanks to innovation from NSK, it is possible to mitigate the effects of this unwanted phenomenon. In a world-first, new NSK
technology is able to stabilise friction whenever the ball screw reverses the direction of motion, significantly reducing the propensity for quadrant glitches.
Circular interpolation is a popular machining operation performed on machine tools such as CNC machining centres and milling machines, as well as EDM (electro-discharge machining) machines. Defined as motion along a circular arc, circular interpolation requires the precise coordination of two machine axes simultaneously. When performing circular interpolation, irregular friction arises when the motion of the ball screw reverses, prompting a deviation from the intended path. These motion errors, known as quadrant glitches, leave micron-level imperfections in the workpiece surface that manifest as undesirable streaks or protrusions.
In sectors such as mould and toolmaking, as well as precision component machining, manufacturers demand ever-higher levels of accuracy and surface finish, which in turn drives the need for better feed performance in machine tools. Software compensation of the servo controller is the common way to address this issue. However, the frictional variation that occurs when the ball screw reverses direction is difficult to predict and software cannot provide full compensation, thus calling for more fundamental improvements in ball-screw technology.
NSK has stepped up to the challenge by utilising in-house proprietary friction control and high-precision evaluation and measurement technologies. The resulting improvements significantly reduce the frictional fluctuations that inherently occur in ball screws when the direction of motion reverses.
By fitting NSK’s new-technology ball screws to machine tools, it will be possible for users to enjoy a higher quality surface finish in the machining of moulds, dies and high-precision components. Ultimately, the technology reduces the time needed for secondary polishing/burnishing processes and contributes to energy savings. Any machine tool performing precision work that requires high-accuracy positioning is set to benefit.